The experience of Gerdau Ouro Branco in digitalizing energy and resources management
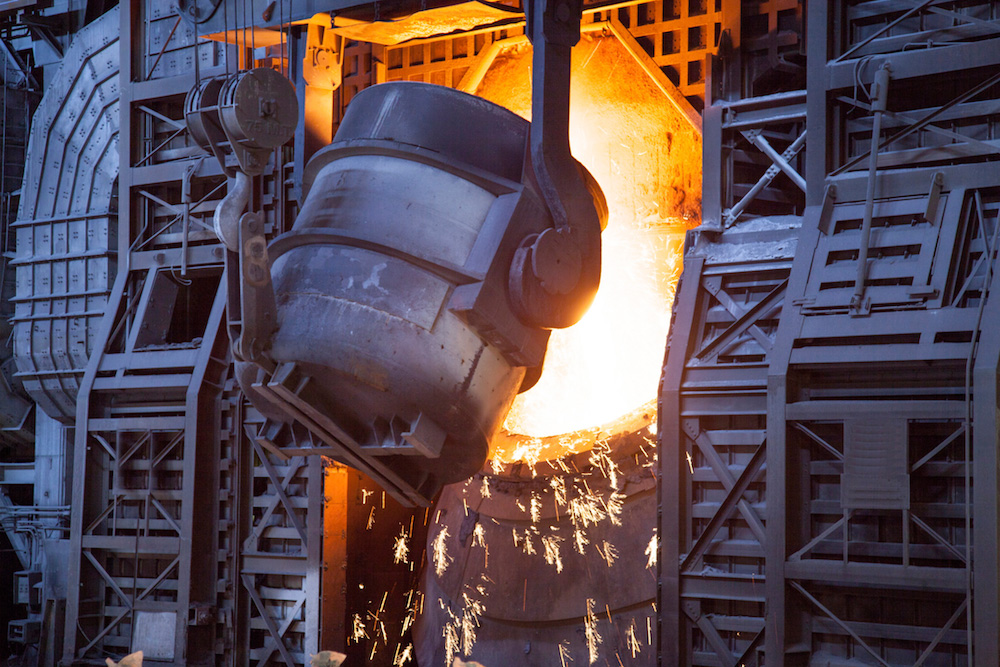
The effective management of energy and resources has become a critical source of competitiveness and sustainability for industrial operations, particularly for the steel segment. Given the complexity and interdependence of its processes, which is often the case of integrated plants, the adoption of digital solutions that enable managing energy performance, improving efficiency continuously, forecasting energy demand, and managing contracts, budgets, and costs becomes an imperative. This article describes the experience of Gerdau Ouro Branco in implementing an integrated energy management digital solution and capturing value from consistent energy efficiency improvements, operational stability, and improved governance.
1 Introduction
In the steelmaking industry, a significant portion of operating costs is related to the use of electricity, natural gas, cryogenics and various other energy sources. Thus, promoting energy efficiency, both in terms of use and co-generation, as well as making operational efforts fit with energy planning and with the management of energy contracts become key to competitiveness. Furthermore, ensuring the effective use of these resources is fundamental to promoting sustainability of the business both in financial terms and in relation to its environmental impact.
According to the World Steel Association[1], the base metals industry invests nearly 20-40% of its total operating costs in energy, a level of use that in 2018 accounted for 12% of the world’s energy usage[2]. At the same time, pressures to decarbonize steel production constitute another major challenge. In 2018, the steelmaking industry was responsible for 7-9% of all CO2 emissions worldwide, which is the equivalent of 1.85 tons of gas for every ton of steel produced[3]. The Carbon Disclosure Project organization[4] has estimated that, on average, 14% of the value of steelmaking companies is at risk with the increase in carbon prices.
Integrated steelmaking plants are highly complex in terms of their production processes, operations and, in particular, their matrix of energy sources. Commonly, dozens of types of energy and utilities are purchased, distributed, consumed and converted into other sources to support hundreds of machines in various production processes. The inherent complexity of this scenario, however, can be matched up with existing opportunities for the rational use of these resources, whether by promoting the efficiency of the processes, by reducing losses, by re-using coke plant, blast furnace and steelworks gases, or by achieving high levels of water recirculation, among other examples[5].
Likewise, the procurement of resources such as electric power, natural gas and cryogenics is governed by supply contracts that have specific rules for pricing, including seasonal factors, minimum limits and fines, among other factors that significantly affect the final costs. In this sense, a proper balance between the demand of production processes for energy resources and their procurement, supply and distribution can also be turned into a major factor for the rationalization of costs.
Taking advantage of such opportunities, however, requires a high degree of coordination, discipline and agility - factors that can be greatly enhanced by digital technologies involving: (1) the acquisition of data on variables related to the production processes, information on production planning and implementation, administrative information on costs and contracts; (2) the processing of those data as indicators of energy yield and the management of that yield; (3) the analysis, modeling and simulation of processes in order to find and implement yield improvement actions; (4) the planning and pricing of the procurement, use and conversion of energy, including the possibility of its co-generation and commercialization; and (5) monitoring of the costs involved at a level of detail suitable for their management.
In order to confront these challenges and increase energy efficiency in integrated steelmaking plants, online monitoring of energy flow data can be used, thus enabling immediate maintenance and improvement of control of the processes and thus avoiding energy losses. In addition, continuous monitoring of emissions can serve to quantify emission and management their means of abatement[6].
Data acquisition, processing and analysis can provide for a better forecast of production process behavior, as well as more intelligent, easier and faster decision-making. A combination of devices equipped with sensors, software and wireless systems, together with a growing capacity for data collection and storage, leads to the availability of new sources of data for modern analytic technologies for faster and more detailed data pre-processing[7].
This article describes Gerdau Ouro Branco’s experience in implementing an integrated digital solution to manage energy and utilities, and in adding value through the reduction of losses, an increase in energy efficiency, and an improvement in management practices for energy and utilities.
2 Discussion
2.1 Energy Management Systems
Energy management systems are defined by the ISO 50001 group of standards as methods and procedures that set objectives, goals and action plans to improve energy yield, including energy efficiency, use and consumption, thus leading to a reduction in costs and emissions, less waste and greater competitiveness[8].
In the case of industrial digital transformation, energy management systems are digital solutions responsible for collecting measurement data from the plant floor and making them available to users by means of graphics, on-line monitoring tools, and energy quality analysis tools that provide for the effective management of the energy resources required for an operation[9].
However, despite the clear benefits, adopting the means of conserving energy and energy management systems faces significant challenges that are common across highly complex entities, as in steel-making. Examples include: low financial viability, uncertainty about prices and future regulations in the energy market, little support from senior management, inadequate prioritization, risks for production and limited authority on the part of the energy manager. Nevertheless, adopting an energy management system can increase the potential for energy efficiency by up to 10%[10].
We should emphasize that one of the main drivers of energy efficiency and energy management is the need to decarbonize the steel-making industry[11].
Energy management systems have a fundamental role to play in the transition to a low-carbon economy and especially so that 2050 emissions goals can be met[12].
In fact, promoting the digitalization of steel-making operations is a fundamental step towards competitiveness in an ever more complex economic environment, where decarbonization and energy efficiency constitute one of the main pillars - especially by the reduction of primary energy consumption, better use of co-generation gases and the management of water resources.
2.2 Implementation
2.2.1 The Management of Energy and Utilities at the Ouro Branco Plant
The Ouro Branco Plant is one of Gerdau’s major capacity units with a wide diversity of production processes, comprised of hundreds of machines which, in turn, use dozens of types of energy sources and utilities.
For the purposes of digital transformation, the Ouro Branco Plant has various sources of data that must be accessed frequently to provide the information required for the goals of managing energy and utilities. In accordance with the nomenclature stipulated by the ISA-95 standard, the Ouro Branco Plant has, merely at Level 2, three different Plant Information Management systems, provided by three different suppliers. Even though all three offer the OPC (Open Platform Communications) interoperability standard, none of them completely covers the plant’s production processes. Furthermore, a set of connected systems developed locally supplements the sources of information with specific functions and data. An integrated view of all the users would only be possible using an application that could ensure connectivity with all of the available sources of data.
The priority of implementing the Energy Management System (EMS) would focus on:
- centralizing the collection and storage of data on energy use and conversion and utilities, as well as relevant production data, including quantities, routes and other data typically found in production orders, recording them in digital versions of the physical and variable measuring devices found in the plant and in the Plant Information Management Systems;
- determine and log energy yield indicators, be they absolute (e.g. kWh, Nm3 or specific (e.g. kWh/t, Nm3/t), including the possibility of stratifying the use of energy and utilities according to pertinent variable in each production process;
- provide balance sheets, warnings, reports and various analytic views to make continuous improvement of energy efficiency and yield possible.
This scope is consistent with Levels 1 and 2 of maturity in energy management proposed by the Ouro Branco Plant Energy & Utilities staff, as shown in the figure below.
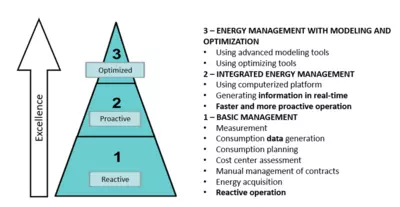
In a subsequent stage, Gerdau will focus on seeking to optimize production processes and configure tools to support its integrated planning, budgeting and costing of energy and utilities, in both the short and long term, as is described at the end of this article.
The architecture of the EMS is given in the figure below, showing the need to integrate various sources of data and the option for a cloud-commissioning model with a Web application.
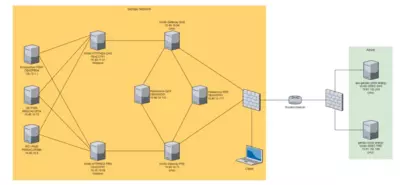
The first phase of implementation required 12 months of design work. The Vetta company (formerly Viridis Soluções en Energia S.A.) was contracted for the supply, implementation and configuration of the system. The numbers below give an idea of the scale and complexity of implementation of the EMS at the Ouro Branco Plant:
- 2,700 variables, representing direct measurements of power, current, flow rates and status, as well as mathematical relationships between those variables (formulas or virtual measuring devices);
- 380 machines and production lines;
- 72 energy and utilities inputs, including primary sources, fuels, industrial gases and air at various pressures, water in various states and by-products.
2.2.2 Routine management, problems and corrective actions
Both the management of energy yield and the performance of actions to improve it require discipline in managerial practices and in the collection and analysis of analysis support data. Such information includes, for example, relevant operating incidents and occurrences that are typical of the level of implementation of the production processes. The EMS installed at the Ouro Branco Plant is used as a single source for the recording, recovery and analysis of that information, making it easier to correlate it with positive or negative fluctuations in the energy yield, and helping promote sustainability and improved efficiency of the processes, as shown in the figure below.
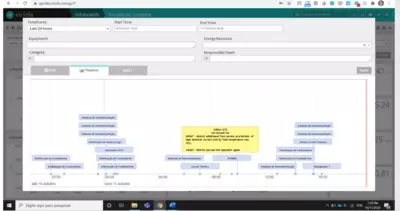
Trouble-shooting (problem identification) is also facilitated by automatic warnings raised by the system via the detection of operating variables with values outside pre- set limits. Warnings are reported to the teams responsible for the operation and maintenance of each process, and contain sufficient semantics to provide for substantial reactiveness in solving problems.
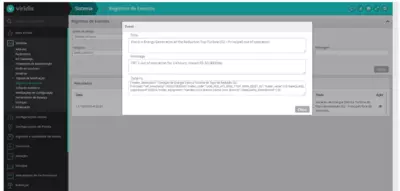
2.2.3 Energy yield management
An important part of the proposed value of a digital solution for the management of energy and utilities is the support for energy yield management, i.e., the monitoring of energy yield indicators relative to pre-set yield goals (or references), the identification of deviations, the proposal of actions to correct those deviations, and verification of the effectiveness of those actions.
A digital system for energy and utilities management must also make it possible to monitor yield indicators over time, thus facilitating the identification of trends and best brands and, potentially, the operating conditions - or context - that produced them.
However, bearing in mind the complexity of the processes monitored and the diversity of context variables, the energy yield analysis must be done not only by measuring the yield observed over a certain period of time, but also by specifying that yield in relation to each condition of interest.
The figure below shows the energy yield analysis of the Ouro Branco Plant steelworks LD converter, but in a format stratified by variables such as shift, class, run, production order, projected and real routes, among various other variables available in the production orders generated by the plant’s production management system.
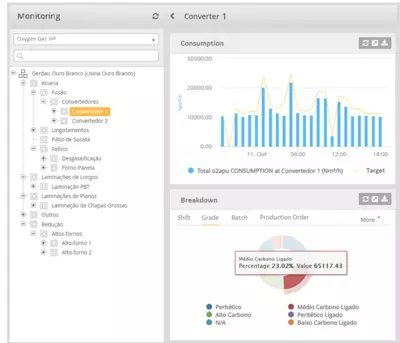
The figure above also illustrates the use of goals - not defined arbitrarily but rather calculated dynamically using forecasting models trained with historical data and fed in real time with information on production and consumption - in the management of energy yield in various operating contexts.
2.2.4 Continuous improvement
One of the main results delivered by an energy and utilities management system is in terms of gains in energy efficiency. A natural means to this is via the identification of processes and machines that are major offenders in terms of energy consumption and yield, and via in-depth analysis of the physical and chemical phenomena of the constructive aspects involved in the operations.
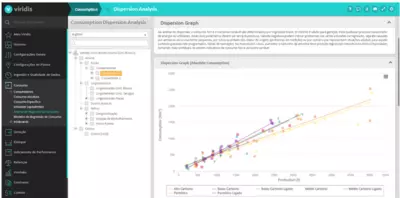
Analyses such as these also make it possible to review yield references (base-lines), which provides for greater adherence to the common yield goals of each process, under each operating condition or context.
2.2.5 Benefits achieved
Deployment of the energy and utilities digital management system at the Ouro Branco Plant made it possible to achieve major quantitative results:
- Operational continuity: The establishment of routines for the continuous monitoring of the levels of cryogenics prevented supply shortage incidents and the consequential interruption of production. Such incidents may have a substantial financial effect of approximately R$ 1.5 million.
- Efficient use of resources: The configuration of automatic warnings and automatic notifications, and the implementation of corrective actions helped stabilize the distribution of argon throughout the plant, thus avoiding the need for vaporization and losses of around R$ 300,000 per incident.
- Reduction of losses: The monitoring of energy yield indicators, such as nitrogen consumption in Blast Furnace 2’s crushed coal injection facility avoided financial effects of around R$ 11 million per day.
In addition, implementation of the system and the resulting adoption of it as a support tool for the effective management of energy and utilities led to significant improvements in terms of agility, transparency and operational safety:
- Connectivity: Integration of multiple sources of data, promoting greater robustness (e.g., by eliminating electronic spreadsheets), agility, transparency and democratization of the information on energy and utilities, with the consequent engagement of various operational teams and areas. In particular, to establish connectivity with all of the Ouro Branco Plant’s PLCs, for both reading and writing variables, the EMS acts as a gateway between various applications, also making it possible to produce important information on the gas operator’s control screens, thus providing his decisions with great agility and assertiveness.
- Quality of the data: Real-time analysis of the quality of the data acquired from the various sources found at the Ouro Branco Plant, with automatic correction of problems typically found in industrial environments: missing data, values outside upper and lower limits, frozen values, abrupt variations, among others - by means of heuristics - interpolation, the use of alternative measuring devices - previously configured in the system.
- Support for exceptional situations: Provision of information on energy and utilities usage in real time, which facilitates operational continuity, especially in exceptional situations, e.g., in the distribution of industrial gases when the steelworks or coke plants gas meters are not available.
- Balancing energy usage and production: Precise monitoring of the process of co-generating energy from industrial gases and from natural gas, making it possible to optimize costs and to better take advantage of the resources of the energy matrix.
2.3 Analysis of the results and future developments
The EMS implemented at Gerdau’s Ouro Branco offers the following groups of functional features:
- Monitoring of the usage, production, emissions and conversions of energy and utilities throughout operations, enabling analyses of the energy yield of assets and improving their energy efficiency.
- Integration of energy yield indicators, goals calculated dynamically from the status of the assets and processes, real-time warnings and dashboards for display and monitoring.
- Tools based on the analysis of historical data(e.g.,MachineLearning) to build advanced models for forecasting and the simulation of critical assets, thus optimizing their operating performance and efficiency.
- Continuous determination of the costs associated with energy and utilities, based on allocation rules that integrate measurement, assets and cost centers, with periodic close out and full integration into the company management systems.
- Management of energy and utilities contracts, taking into account seasonal rates, orders contracted, take-or-pay, fines, and taxes, among other commercial factors, with integrated control and implementation processes.
- Preview, simulation and optimization of the usage and production of energy based on production plans, with analyses of scenarios, sensitivity analyses and the quantification of operational and financial risks.
- Orchestration of the process of preparing the energy and utilities budget plan, with the possibility of optimizing usage and distribution plans for energy inputs as a function of the current contracts.
The scope of the first phase of the implementation project, which accounted for all of the quantitative and qualitative results presented in the previous section, included only items 1 and 2 in the list above.
In fact, with the delegation of basic tasks: data collection, calculation of energy yield indicators, processing of energy bills, among others - to the digital energy management system implemented at the Ouro Branco Plant, the specialists were able to devote their time to analysis activities and actions to improve processes that effectively create value for the organization. This dynamic creates a virtuous cycle of analysis, outcomes and maturity of judgement that contributes to the competitiveness and sustainability of the results. It is not by happenstance that ISO standard 50001 applies directly the systematization of this cycle, promoting the development of administrative maturity and the addition of value.
The next stages of implementation will seek not only to supplement the strategy presented in Figure 1, but also to make possible applications such as:
- developing sophisticated analytical models, capable of simulating and optimizing the distribution of critical resources with co-generation gases, so as to balance out the supply, demand for and co-generation of energy at a minimal cost[13];
- predicting the demand for energy and utilities over the short and long term, integrating operational decisions on the start, intensity and end of production processes with their respective financial effects estimated from the terms of supply contracts for electric power, natural gas, cryogenics and other inputs[14];
- digitalizing the entire cycle of energy planning, budgeting (including pricing for energy contracts) and costing, as described above;
- configuring tools to determine the carbon emissions of each of the main production processes used at the Ouro Branco Plant, making it easier to report sustainability and assess impacts and opportunities;
- extending the digital energy and utilities management solution to other units of the Gerdau group, bringing them into a unified data base and making it possible to identify better brands, share best practices and explore the synergies inherent in the organizational complexity.
We should emphasize that adoption of the system was made considerably easier by factors such as: (1) greater robustness compared to the use of electronic spreadsheets produced and maintained separately, (2) the quality of the data, indicators and reports produced by the system, (3) ease of use, (4) adherence to the energy and utilities yield management and continuous improvement routines in use at the Ouro Branco Plant.
3 Conclusion
Digital systems for the management of energy and utilities have great potential to improve not only the maturity, but also the results achieved by more robust and frequent management practices. Such practices involve the collection and processing of energy usage data, the determination and analysis of yield indicators, and the identification and implementation of opportunities for continuous improvement in energy efficiency, planning and governance.
The implementation of an energy management system at Gerdau’s Ouro Branco Plant provided a series of quantitative and qualitative benefits, made viable by the integration of various sources of data and by consistent actions on the part of the Energy and Utilities staff, who combined their technical knowledge with the analytic capacity and agility provided by the system. Such results are consistent with the recommendations of ISO standard 50001, since they implement controls and procedures intended for the routine management of energy yield and its continuous improvement in a sustainable manner.
References
[1] World Steel Association: Energy use in the steel industry. 2019 [accessed 15 October 2020]. Available at www.worldsteel.org/publications/fact-sheets.html
[2] Sendich E, U.S. Energy Information Administration [www.eia.gov/] The basic metals industry is one of the world’s largest industrial energy users [accessed 15 October 2020] Available at www.eia.gov/todayinenergy/detail.php?id=38392
[3] Carbon Disclosure Project: Steel Sector Faces Significant Losses From Future Climate Regulation. 2019 [accessed 15 October 2020]. Available at www.cdp.net/en/articles/media/steel-sector-faces-significant-losses-from-future-climate- regulation
[4] World Steel Association: STEEL’S CONTRIBUTION TO A LOW CARBON FUTURE AND CLIMATE RESILIENT SOCIETIES. 2020 [accessed 15 October 2020]. Available at www.worldsteel.org/en/dam/jcr:7ec64bc1-c51c-439b-84b8- 94496686b8c6/Position_paper_climate_2020_vfinal.pdf
[5] Wang R, Jiang L, Wang Y, Roskilly A. Energy saving technologies and mass-thermal network optimization for decarbonized iron and steel industry: A review. Journal of Cleaner Production 2020;274:1-28.
[6] Murri M, Streppa E, Colla V, Fornai B, Branca T. Digital Transformation in European Steel Industry: State of Art and Future Scenario. New Skills Agenda Steel: Industry- driven sustainable European Steel Skills Agenda and Strategy [internet]; 2019 [accessed 15 October 2020]. Disponível em www.estep.eu/assets/Uploads/Technological-and- Economic-Development-in-the-Steel-Industry-ESSA-D8.1.pdf
[7] Branca T, Fornai B, Colla V, Murri M, Streppa E, Schroeder AJ. The Challenge of Digitalization in the Steel Sector Metals. 2020;10: 288
[8] NBR ISO 50001:2011 – Energy Management Systems – Requirements with Guidance for Use. Rio de Janeiro: Associação Brasileira de Normas Técnicas; 2011.
[9] Yahyaoui I. Advances in Renewable Energies and Power Technologies. 1a ed. Elsevier Science; 2018
[10] Brunke J, Johansson M, Thollander P. Empirical investigation of barriers and drivers to the adoption of energy conservation measures, energy management practices and energy services in the Swedish iron and steel industry. Journal of Cleaner Production 2014;84: 509-525.
[11] Wesseling J, Lechtenböhmer S, Åhman M, Nilsson L, Worrell E, Coenen L. The transition of energy intensive processing industries towards deep decarbonization: Characteristics and implications for future research. Renewable and Sustainable Energy Reviews 2017;79:1303-1313.
[12] Allwood, J. Steel, aluminium and carbon targets: alternative strategies for meeting the 2050 carbon emission targets for steel and aluminium. Proceedings of the R'09 Twin World Congress: Resource Management and Technology for Material and Energy Efficiency; 14-6 Setembro 2009; Davos, Switzerland.
[13] Qi Z, Jiu-ju C, Jun S, Wen-chao L. Study on Energy Efficiency and Energy Management in Integrated Iron and Steel Works. Proceedings of: International Conference on Energy and Environment Technology; 2009; Guilin: 2009 p. 341-343.
[14] Marchiori F, Belloni A, Benini M, Cateni S, Colla V, Ebel A, et al. Integrated Dynamic Energy Management for Steel Production. Journal of Cleaner Production 2017;105: 2772-2777
Authors:
Eder Quental de Araújo, José Geraldo Moreira, Patrick de Castro Andrade, Bruno S. Pimentel, Thiago Turchetti Maia, Fernanda Drumond, Marcelo P. Kelles