Simple application of smart sensors in a small section mill
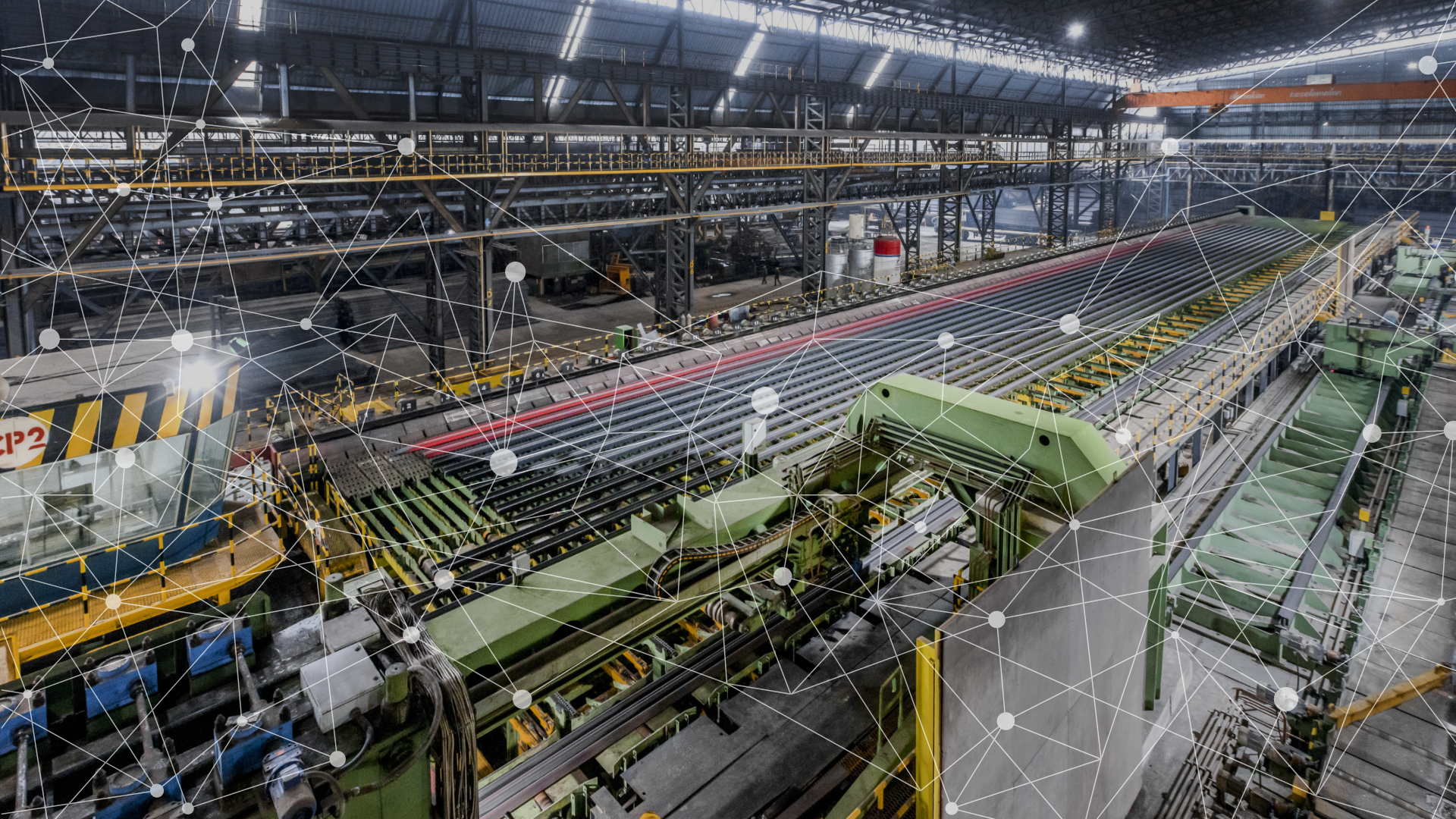
Fast realization of a customized solution
The 5G/IIot-Smart Sensors team within our Asset Optimization unit has set itself the goal of implementing a modern digital infrastructure at customer sites by utilizing the new possibilities of the Industrial Internet of Things (IIoT) and smart sensor technology.
In this context, the customer requested a system for monitoring the 80 idler rolls in the inlet area of the cooling bed of a small section mill, whether they rotate or stop turning due to blockages resulting from dirt in the bearings. Individual roller blockages can cause damage to the product, which is usually only detected at a very late stage, leading to high costs. In addition, a manual inspection of the rollers is very time-consuming due to the poor accessibility.
The solution
As part of the proof of concept (PoC), a "simple" solution was developed to monitor these rolls without making any changes to the existing automation or IT infrastructure, i.e., no new cabling etc. A complicating factor was that the high surrounding temperature in the area of the rollers was as high as 250 degrees.
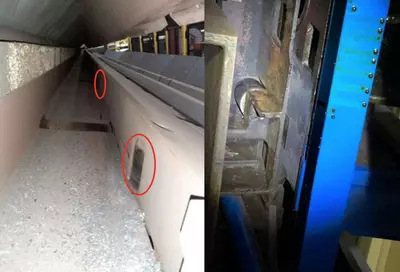
Given the location of the installation, various measurement technologies could not be used, so we concentrated on inductive and optical methods, whereby the rotation was to be detected via drilled holes in the roll material or by contrast changes using a light sensor.
Data visualization with DataXpert
To keep investment costs low, an IO-Link master was used in conjunction with an edge device with a 4/5G M2M connection. The edge device processes the sensor data and sends it via MQTT over the M2M connection to an accessible MQTT broker into our DataXpert cloud, where we can then visualize and evaluate it with the DataXpert tools.
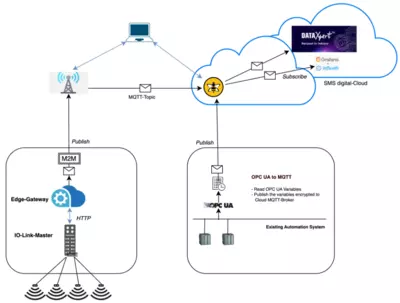
DataXpert is a unique software tool used to correlate condition data with automation process data and thus enable online predictive maintenance. DataXpert is based on RulesXpert, which transforms expert knowledge in digitalization and turns this information into actions by creating rules that correlate condition and process automation data. When these rules are applied in practice, integrated into an online database, and work as intended, a finished predictive model programmed in Python, R or Julia can be directly applied. The rule becomes predictive after 2-3 months. In this way, it is possible to overcome the challenging task of predictive maintenance within a short time by engineers working in the plant.
We prepared the sensor technology and the edge device, which was installed in a field cabinet and set up on site at the customer, and then we attached the sensor technology and connected the box.
The results
The results were very surprising. The customer greatly appreciated that this technology could be realized in such a short time. Instead of receiving a "roll is running"/"roll is not running" message, as requested by the customer, we saw a detailed acceleration and deceleration behavior of the rolls coupled with process data.
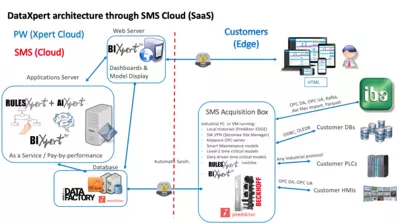
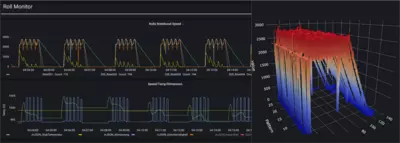
The recorded curves are evaluated by data scientists, which enables the behavior of the rolls to be monitored and therefore failures to be predicted. In addition, recommendations can be made for maintenance in areas of the cooling bed where the rolls should be checked or replaced.
The customer asked us to correlate this new data with his automation data. To do this, we acquired the relevant data (speed, temperature, material, etc.) via OPC from the existing automation and posted it to our cloud via MQTT.
Based on this successful PoC, the remaining 76 rolls of the cooling bed will also be equipped with this technology to exploit the potential of smart sensor monitoring.
Conclusion
The 4/5G edge technology in combination with smart sensor technology offers great potential, especially in retrofit environments. Areas that previously could not be included or only with great effort can now be monitored. It also offers customers new opportunities to improve their production and reliability levels through machine learning, etc., without having to adapt the existing automation and IT infrastructure.